OCT scanning head
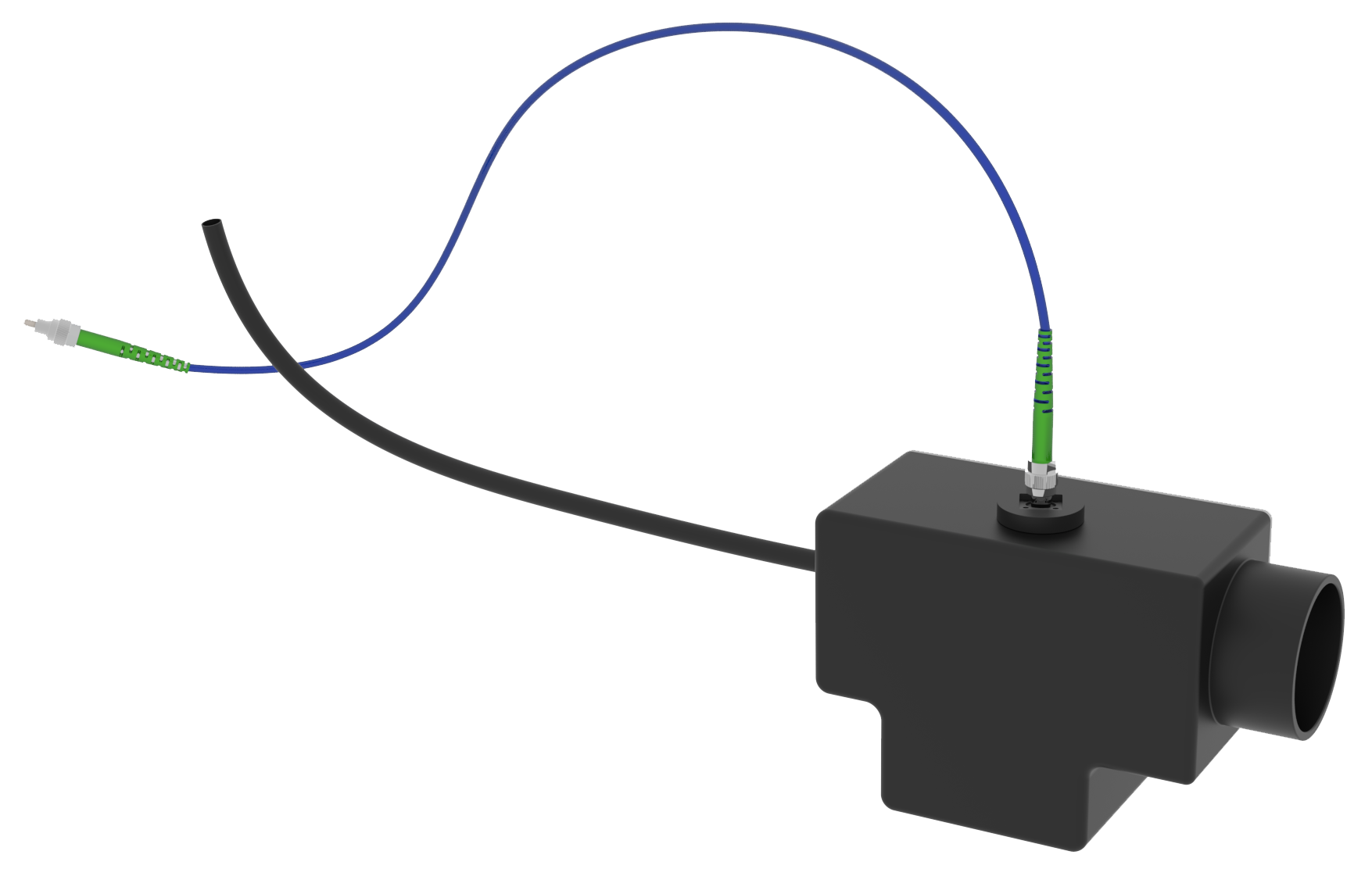
Scanning head
The scanning head assembly provided by our company includes: optical fiber collimator, two-dimensional scanning galvanometer, scanning lens group and zoom lens; The scanning head assembly is used in the optical coherence tomography (OCT) laser scanning imaging system.
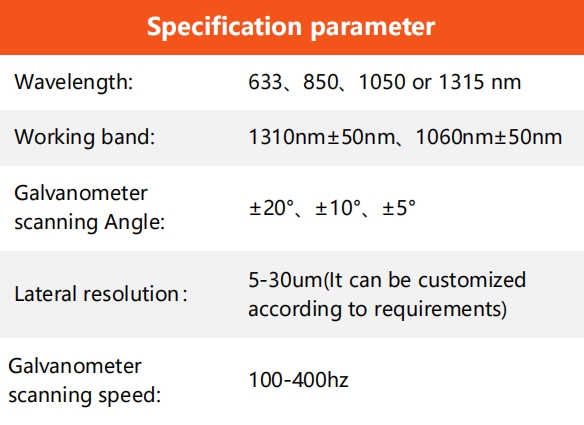
Four major characteristics
Telecentric scanning lenses are crucial for OCT and other laser scanning imaging systems because when the laser beam scans the sample, they produce a flat imaging surface.
Wide-field imaging technology achieves the imaging of objects within a relatively large field of view through methods such as optical design and image processing.
Low f-theta distortion generates geometrically corrected images without the need for a large amount of post-image processing.
The combination of the OCT scanning head and the self-built microscope can significantly expand the system's functions, especially in multimodal imaging and cross-scale observation (surface + deep) scenarios, where the advantages are prominent.
Working principle
In optical coherence tomography (OCT) and other laser scanning imaging systems, the laser beam incident on the back of the aperture (entry pupil) of the lens is scanned at a certain range of angles. The scanning lens converts the position of the light spot formed in the image plane of the lens field of view. Telecentric scanning lenses are designed to generate uniform spot sizes at each scanning position on the imaging plane, and this method can form high-quality images of the samples. Generally, a laser scanning microscope system is equipped with a scanning lens with a sleeve lens, thereby generating an optical system with infinity correction. However, most OCT systems are designed for scanning lenses without scanning sleeve lenses.
When designing an imaging system using LSM scanning lenses in OCT configuration, it is important to adjust the design wavelength, alignment distance, scanning distance, entry pupil and scanning Angle specifications to maximize imaging quality. For example, the larger the diameter of the incident light, the smaller the size of the focused light spot. However, due to vignetting and/or increased aberrations, the range of the scanning Angle decreases as the beam increases.
For a single galvanometer system, the center of the scanning lens’s entry pupil coincides with the pivot point of the galvanometer. When using a single galvanometer, the scanning distance is measured from the mounting surface of the lens to the pivot point of the galvanometer. As shown in Figure 1.
If the imaging system uses two galvanometers (one for scanning in the X direction and the other for scanning in the Y direction), the entry pupil is located between the two galvanometers, as shown in Figure 2. The scanning distance is the distance from the installation surface of the lens to the nearest galvanometer pivot point to the lens (d1) plus the distance from the galvanometer pivot point to the entry pupil (d2). It is very important to minimize the distance between the two galvanometer lenses, because when the entry pupil and the beam control pivot point do not coincide, the imaging quality will decrease. This is mainly due to the change in the optical path caused by the beam scanning the sample. Figures 1 and 2 respectively show the imaging systems containing one and two galvanometer mirrors.
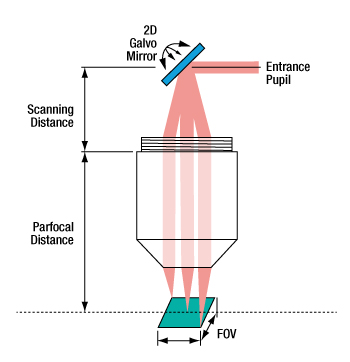
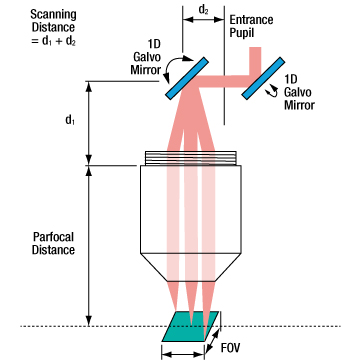
Figure 1 shows that when using a galvanometer, the entry pupil is located at the pivot point of the galvanometer.
Figure 2 shows that when two galvanometers are used, the entry pupil is located between the two galvanometers.
The definition of customizable parameters is acceptable
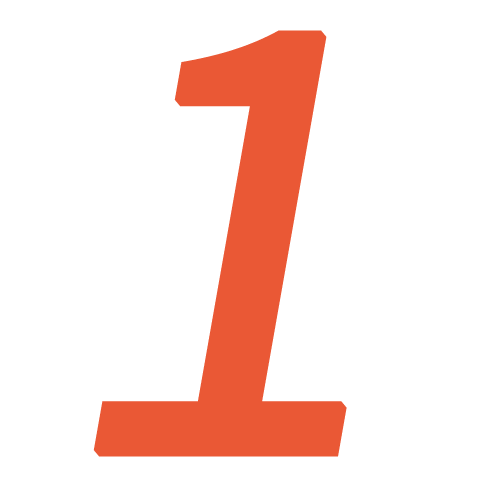
Equal focal distance (PD
PD is the distance from the installation plane of the scanning lens to the front focal plane of the scanning lens.
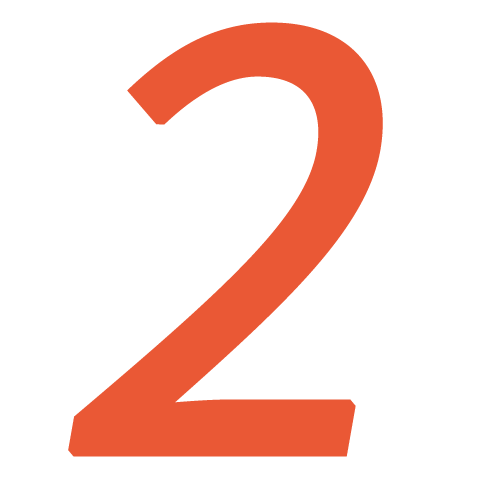
Working distance (WD or LWD)
The distance between the tip of the scanning lens housing and the front focal plane of the scanning lens is defined as WD.
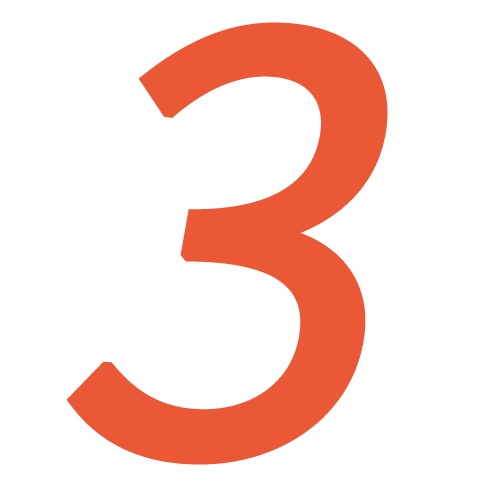
Entry pupil size (EP)
If a single galvanometer is used, the entry pupil (EP) is located at the pivot point of the galvanometer. When two galvanometers are used, EP is located between the two galvanometers. The size of EP is specified as the diameter of the parallel laser beam that maximizes the resolution of the imaging system.
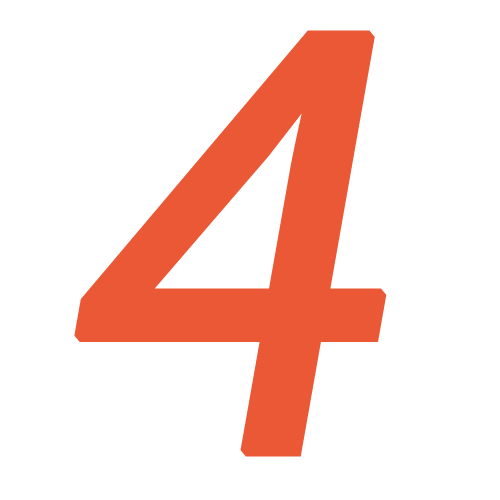
Scanning Angle (SA)
The laser beam reflected by the galvanometer is incident on the lens at a certain Angle. The Angle measured based on the optical axis of the lens is the scanning Angle. The maximum allowable scanning Angle range is listed in the specification sheet.
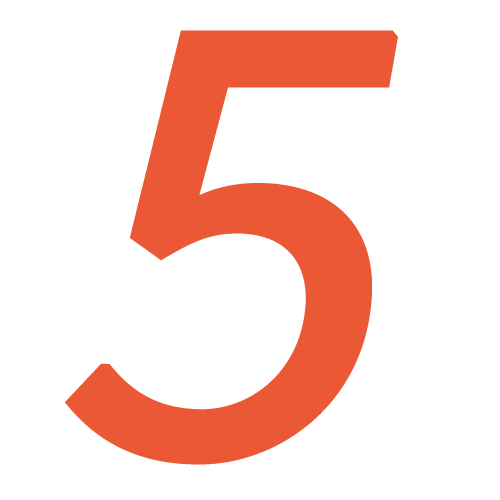
Field of View (FOV)
FOV refers to the maximum area size at which the resolution of the image formed on the sample is the same as or better than that specified by the scanning lens. An appropriate utilization rate of the scanning lens is assumed in the optical system. During the operation, the position of the scanning point is in the field of view.
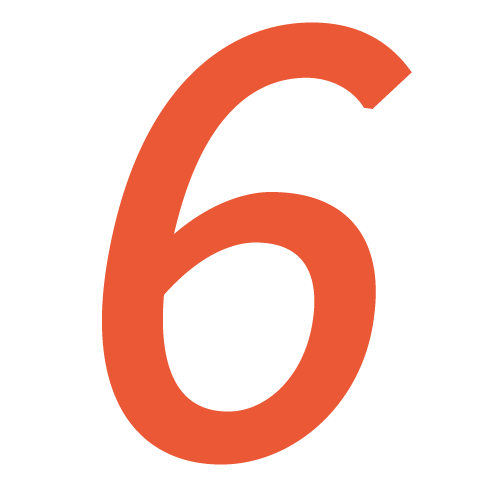
Scanning distance (SD)
SD represents the distance between the aperture planes, that is, the entry pupil position, and is defined as the back of the objective lens mounting plane where the threaded base is installed. Regarding these lenses, the installation planes are adjacent to those threads or thread planes of the lenses. When two galvanometer lenses are used, an aperture plane appears in the middle of the two galvanometer lenses. When using a galvanometer, the pivot point of the single galvanometer coincides with the plane of the aperture.
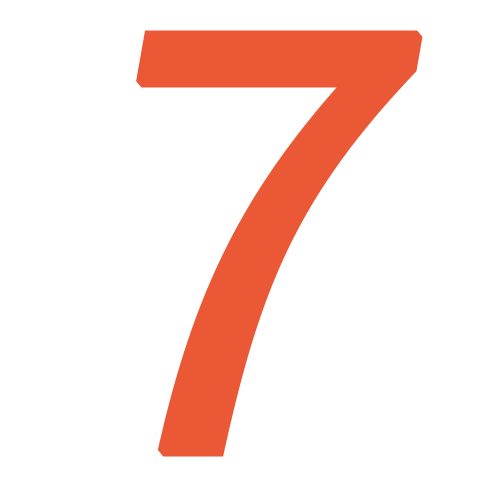
Depth of Field (DOV)
The DOV parameter corresponds to the distance between the parallel planes on both sides of the front focal plane, and the beam spot diameter of this plane is √2 times that of the front focal plane. As a general example of OCT, this parameter is useful in the design of optical systems when sleeve lenses are not used, at which point the front focal plane is also the sample plane. When the sleeve lens is used in combination with the scanning lens, the image plane is located between the scanning lens and the sleeve lens. Then, the depth of field at the sample is controlled through the objective lens of the microscope.